

|

|
Part 4: On the
Factory Floor
Made in Rivers
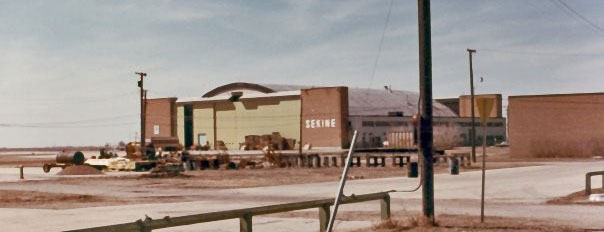
The mandate of Sekine Canada Ltd.
was to start a Canadian made bicycle company which would operate,
subsidized by the Canadian government, for ten years, after which the
company would be on its own.
Basically it started as an assembly plant. Bicycle frames, forks,
and other parts were shipped from Japan and brought by rail to the
hangar. Parts were inspected then sent to work stations. Assembly was a
mixture of skilled labour and mechanization. For example, on the wheel
assembly line spokes were inserted into hubs which were then laced by
hand into rims. A machine then automatically tensioned the 36 spokes in
15 seconds.
Another interesting apparatus was the wheel-truing machine. It took
skill to adjust it for different rim sizes but was a marvel of
automation.
A worker had to lay a wheel into the machine where a press held the hub
in place. Within seconds the machine simultaneously used 36
screwdriver-like bits around the circumference of the rim to tighten
all the spoke nipples to a specific torque. The final truing
adjustments were done by hand.
Separate stations assembled handlebars. An assembly line moved upturned
frames along a conveyor as components were attached. Quality control
inspections were a key element of the process, before packing and
shipping was completed.
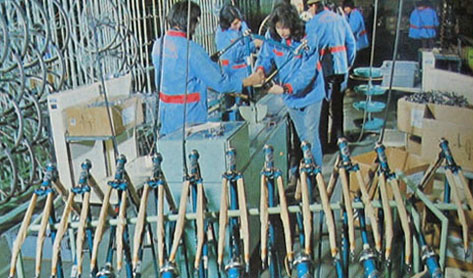
Hard at work at the Sekine Canada plant
In the beginning, they enjoyed
great success and their bikes soon became known for their excellent
quality. Frame paint was electrostatically applied, resulting in
a superior overall finish. Attention to detail and considerable
pre-assembly work made them a pleasure to assemble at retail outlets.
It was quite possible to set up a new Sekine in approximately half the
time of similar competing brands. The quality surpassed that of its
major competitor of its day, the Canadian Cycle and Motor Company
(CCM). They provided serious competition to that one time premier
bicycle manufacturer, and were often better made than many of the
bicycles being imported during the "Bike Boom" era.
Canadian made Sekine bicycles were distributed throughout North
America, with sales as far away as Hawaii and Alaska, and were readily
available in most major centers across Canada.
Bart Lavallee remembers visiting the Sekine Plant as a boy and admiring
the bikes displayed in a showcase by the entrance and remembers his dad
buying him the shiny new 10 speed. He is still in possession of a
Girl’s Sekine and say the finish is as bright as new.
A Superior
Product
That the Sekine
bicycle was known as a quality product should come as no
surprise. In the early seventies, the Japanese business machine
was focused on quality and quality assurance. Bicycles were just
one of countless excellent products being exported by Japan. It was
under the supervision of Japanese quality engineers that Canadian
Sekines were built.
This meant that the bikes were always a cut above. It was not
uncommon to hear local bicycle shop (LBS) owners comment positively on
the quality of the bicycle and its presentation when they arrived at
the shops. For example, Sekine was the only company that offered
a road bicycle with the handlebars already wrapped with handlebar
ribbon.
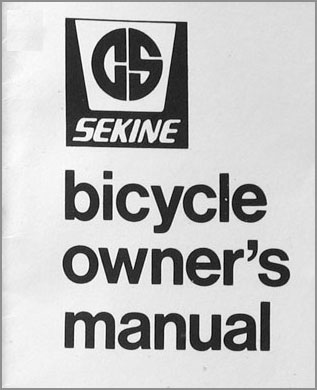
Each bike came with a 15 page manual with assembly, safety and
maintenance instructions.
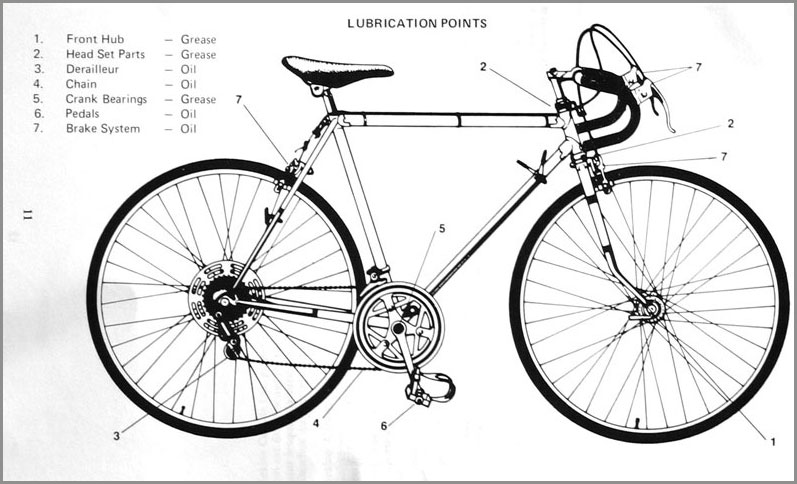
And, forty years later, the quality built into the
bicycles still shows.
Like its competitors, Sekine targeted all levels of road bicycling
interest, from the SHA, the bottom of the line model, barely a step
above the upper end department store bicycles, to the impressive and
extremely well presented Sekine SHX.
The SHX 270 was the top of the line. It was available only by
special order and featured superior components throughout. The
SHX was the only Sekine, from the early line-up, to be offered with
tubular wheels.
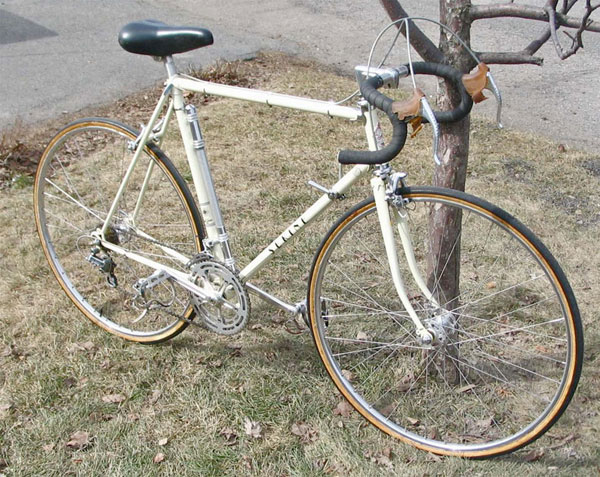
SEKINE SHX 270:
The bicycle was light, sleek and
attractive, but never achieved much of
a following.
It was
designed for competition and, as such, was not a comfortable
bicycle to ride recreationally. But, as collectible
bicycles go, the Sekine SHX is one of the most desired of the Canadian
made vintage road bicycles. They are rare and well fitted
bicycles that shine with a dignity that they deserve.
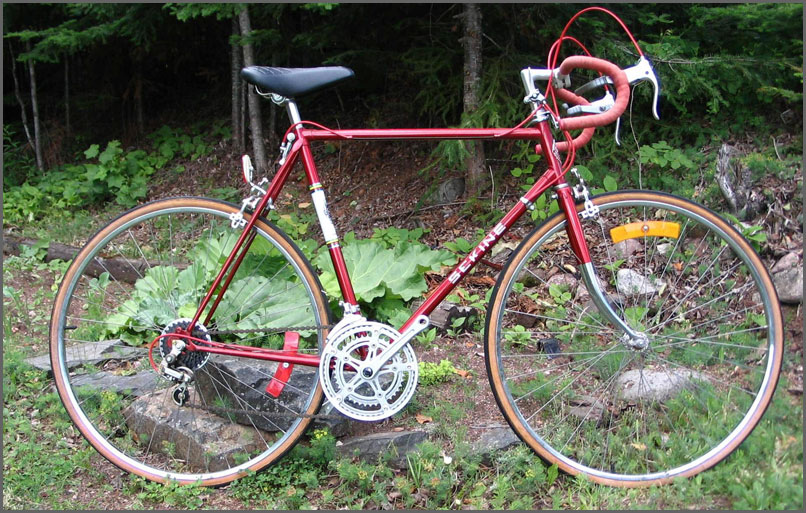
The Sekine SHC 271
The more basic Sekine bike was not as special, but a quality ride all
the same.
With the appearance of the SHC and
lesser series, we see the disappearance of the exotic tube sets
featured on the more sophisticated Sekine bicycles. Gone also is
the chrome plating found on the SHT and SHS models.
Though the SHC 271 was equipped with quick release wheels, the alloy
rims were replaced by the much heavier and less effective steel
units. Other steel components added even more weight.
Despite the slightly lower quality of the materials, The SHC 271 is a
very nice recreational bicycle that offers a lively ride. It will
please all but the most demanding vintage road bicycle rider. And
once again, like all Sekine bikes, the finish and art is just great,
durable and pleasing to the eye.
The lower end models did, however,
sport a unique and often times well remembered head badge containing a
single rhinestone. Many of the people, whose interest focused on
ten speeds in the those days, fondly remember this unique badge and
often go on to comment on how good the Sekines, of their day, were.
All in all, the lower end Sekine was a well-made bicycle that could be
had for a modest price, unlike its more sophisticated brother, the SHX
that sold for $439.95 Canadian in 1976.
A Guarantee - signed by
Mishio
Kumouri, Plant Manager, remained in Canada and now lives in
Winnipeg
The
distinctive headbadge with its iconic rhinestone.
Some will find it interesting that after all the years that have passed
since the last Canadian Sekine rolled out of the plant at Rivers, that
one of the more prominent features remembered was a piece of costume
jewelry, glued into the Sekine headbadge,
The rhinestone
headbadge was usually fitted to early Sekines, those
manufactured prior to about 1975. After that, or some other very
close to it date, the Medialle badge came into being. Though not
a memorable as the incredibly unique rhinestone model, the Medialle
badge did, none the less, scream vintage, thanks to its ornate
appearance and cut out windows. Truly an item to help set the
Canadian Sekine apart.
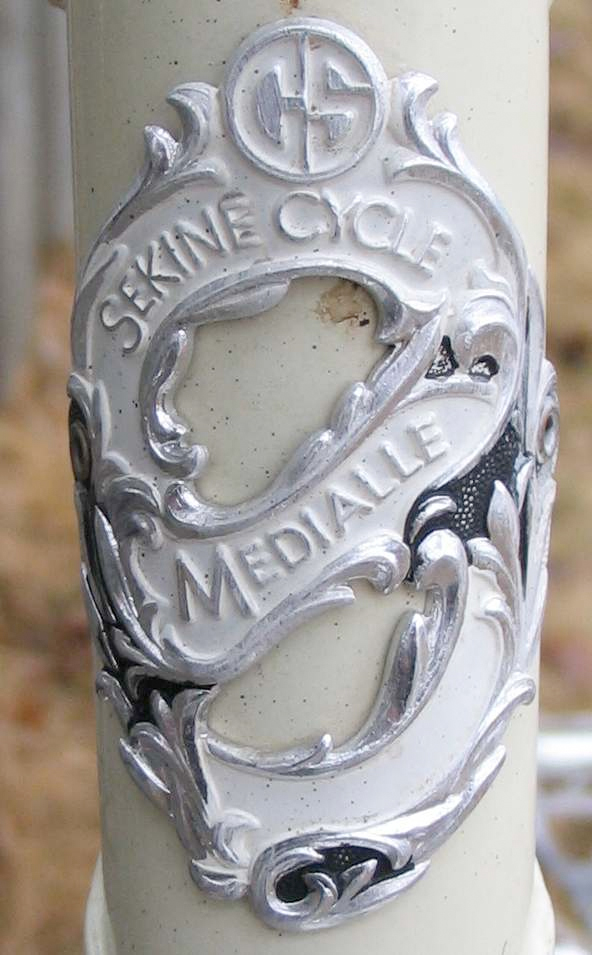
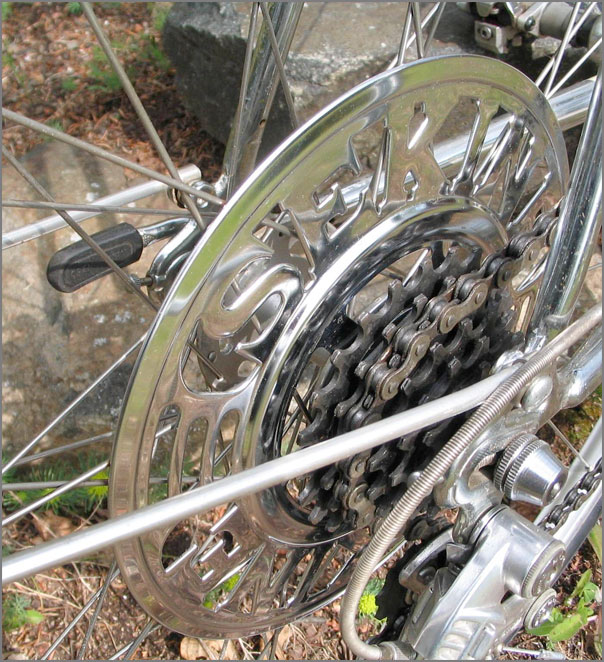
Another iconic feature was the ornate Sekine rear spoke
protector…
Of course these cosmetic add-ons
were pure marketing attempts. It seems they were a success in
they remain in the minds of people nearly half a century later.
The appearance of the Canadian made Sekine changed some time after the
middle of the 1970s as did model names and the range of models offered.
Art work became simpler and most chrome plating on frame sets was
eliminated. Fork blades, on some of the higher end models, did retain
the chrome blade ends
The 1979 suggested price list ranged from $1854 to $899.
On The Factory Floor
The daily operation of the Rivers Sekine factory was unique in several
ways. The manufacturing work was carried out largely by
participants in the Lifeskills /Job Training program of the
Oo-za-We-Kwum Centre and was supervised by highly trained Japanese
engineers. Most of them resided in the former base housing almost
adjacent to the factory building. The components were made in Japan,
although there were plans to begin sourcing some part from Canadian
manufacturers.
The main focus was to take those quality parts and assemble them in a
manner that assured the consumer of a reliable, highly functional, and
attractive piece of machinery. As we have said, these bikes were about
much more than simple transportation. They were designed to inspire
pride of ownership and lasting service.
The whole process from upper management down to the factory floor
seemed ideally suited to produce the desired results.
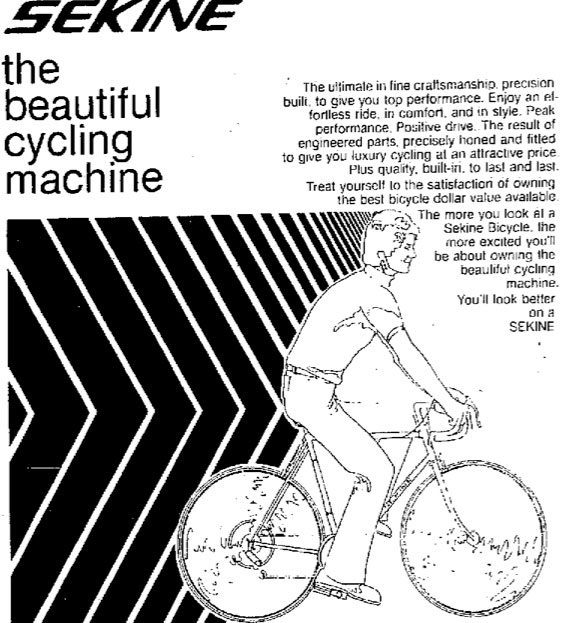
A Sekine ad from June 10, 1974 in the Winnipeg Free
Press.
Factory Photos 1978
The following illustrate some of the factory operations that went into
producing a quality bike,
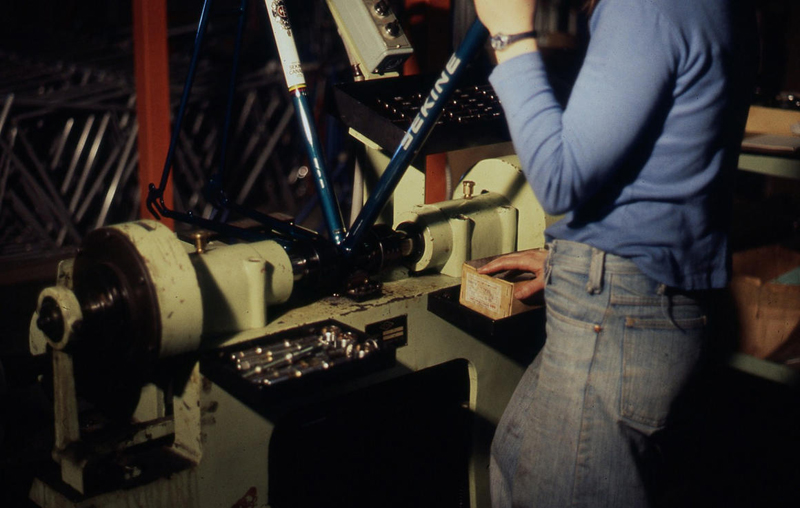
Work on the assembly line requited precision.
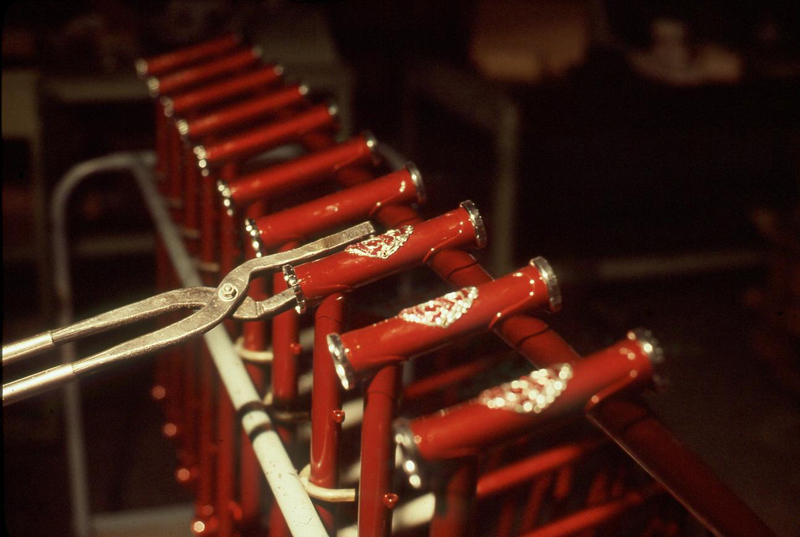
Applying the iconic decal.
Fork installer - Highly skilled precision work was essential at every
step.
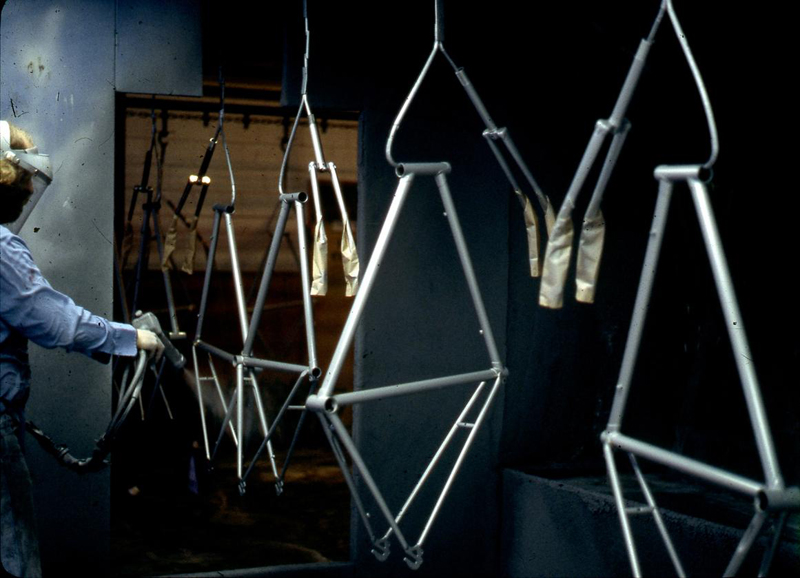
The paint shop – vital to the appearance of the finished product and to
its longevity.
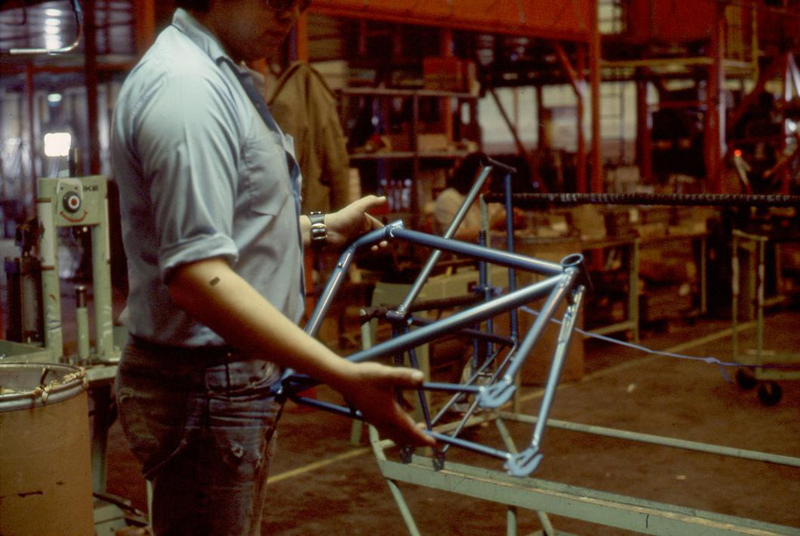
Inspection was the vital final step in each phase.
Promotional photos from the catalogue.
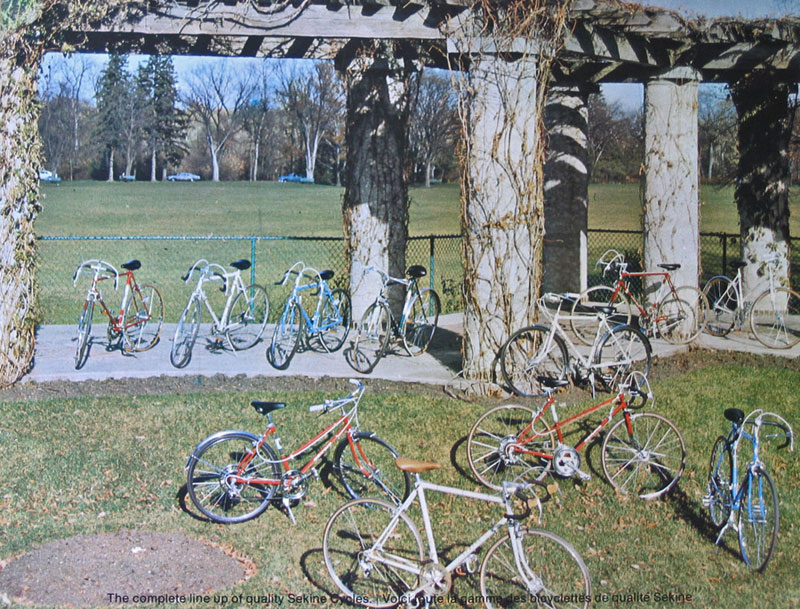
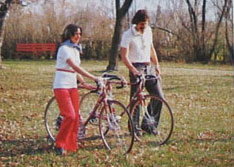
One of a series of promo shots in the Catalogue, likely all shot in our
region.
Life on the Factory Floor
Some Memories from Dave Cluney…
The plant was important for a number of reasons, one being that local
jobs were an asset to the community. His dad was a production Manager
at Sekine and Dave worked in the welding shop brazing bike frames.
Dave has one of only 12 Sekine 5 Speed Touring Bicycles made at the
plant. 5 went to the US 7 that remained in Canada.
These bikes were deluxe in every way. They had brake lights and
signal lights that flashed in a sequence of three bulbs, like some of
today’s cars. They came with AM radio and their own special Tire Pump
(to fit the Japanese made tubes.)
He bought it when the plant was closing, and selling off
everything. It was the last one available, displayed in the
showcase that was located on the second level of the factory.
As with all Sekines, the workmanship and materials were excellent.
He recalled an interesting incident from his first day on a job. There
were three supervisors in charge, each of whom who spoke limited
English. He was shown the work station and one manager showed him
how to adjust the torch used for brazing the tubes together to assemble
the frame. A little later the second manager came by and told him to
change the adjustment of the torch. Later still the third manger came
by and asked him to change the setting again. Finally the first manager
came back and reprimanded him for changing things.
The mixture of local workers, Aboriginal workers from other communities
and Japanese supervisors, made the operation unique and no doubt was
beneficial as a cultural exchange. More than one of the Japanese
workers, stayed in Canada and a few married girls from the nearby Sioux
Valley Reserve (Now The Sioux Valley Dakota Nation).
He remembers a man named Yamota as being the “Head Guy”.
The giant hangar that became the factory was the largest structure on
the base, built to accommodate the huge twin bladed “Vertical
Lift Helicopters ” that were used in Canada’s First Helicopter Squadron.
Another Personal Experience
Twenty six year old car mechanic, Mr. Mamiya was one of eight workers
who cam from Japan to the Oo-Za-We-Kwun Centre in July of 1973 to turn
a vacant aircraft carrier into a bicycle factory. Looking back, he
remembered that summer as “a lot of fun”. He and other workers
rented a house from among the hundreds available that used to house
military personnel.
Once the plant was operational he became the maintenance man and was
responsible for making sure that the assembly machines ran properly.
In his spare time he enjoyed summer activities such as camping and
swimming, and although he tried curling he remembers our Manitoba
winters as a time when he preferred to stay indoors.
Workplace memories included operating the electric forklift and the
difficulty encountered when one had to drill into the high-strength
concrete floor that was designed to support huge aircraft. Mr. Mamiya
and other Japanese workers left in 1979, and he took with him the
custom 1974 red Sekine SGT bike that he had brazed together himself.
The Sekine Frame Shop – 1977
For some Sekine employees in Japan, the opening of a branch plant in
Canada provided an opportunity for advancement, or perhaps an
opportunity for adventure.
In 1975 Mr. Seki, a young engineer, applied for a supervisor position
in the Rivers operation. The plant was just beginning to prepare
for expanding, and for the local manufacturing of the frames. Seki
spent a year in training in Japan before his arrival at Oo-Za-We-Kwun
in June of 1976. He took over the frame shop and was responsible for
training and supervising welders, as well as quality control and
productivity. The frame shop grew to 14 skilled employees and was
making 200- 250 frames per day.
He was very busy. It was hard work. The shop was hot and poorly
ventilated. Frame brazing releases harmful gasses. Like several
of the other Japanese workers, he stayed in Canada after the plant
closed. Mr. Seki and a few friends rented a truck and headed for
Vancouver.
Thanks to the Sekine Zine for the previous two items.

|
|